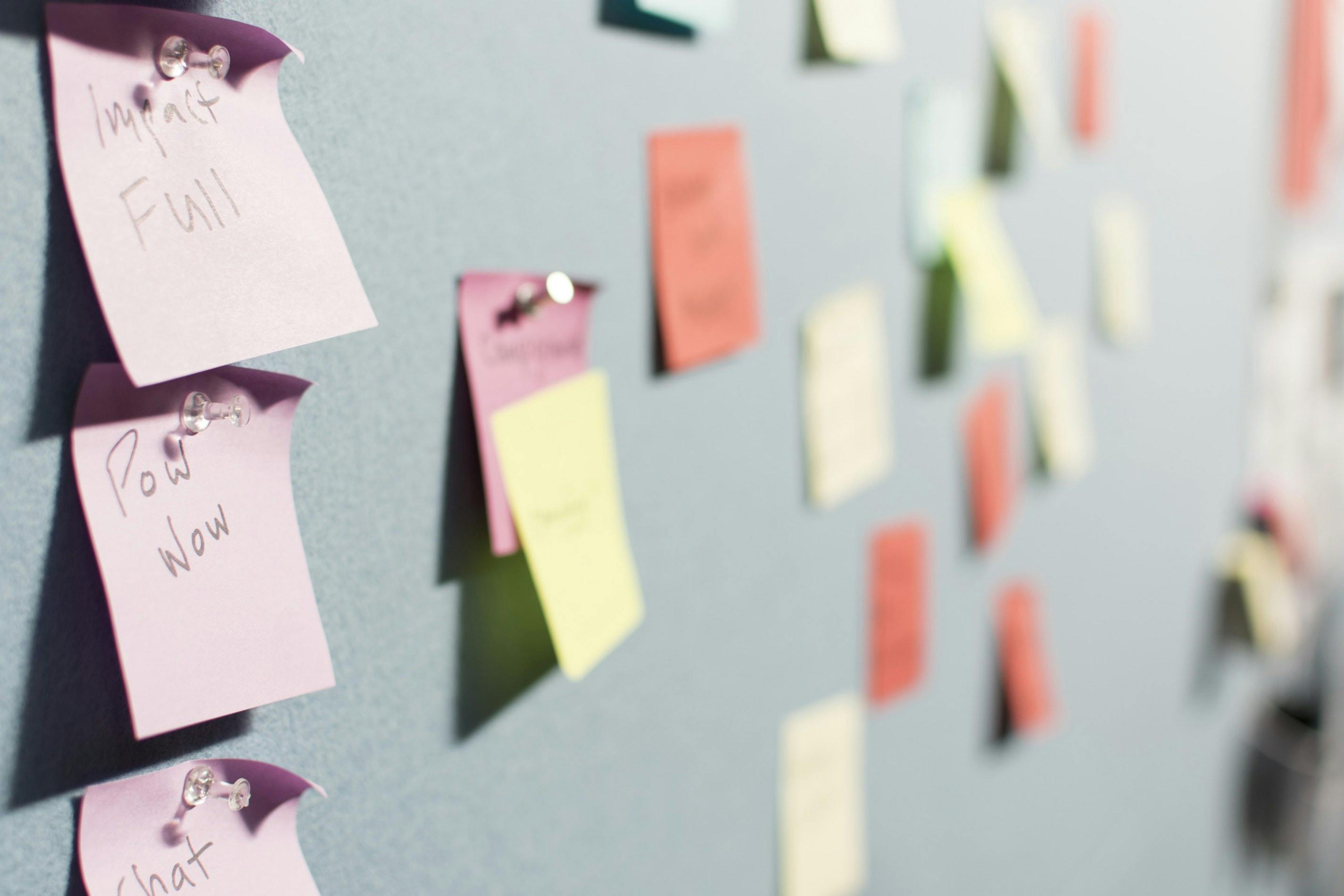
Automation can drive huge impact for professionals and business of all sizes. On the last posts in this series, the importance of Automation was highlighted and showcased with a case study. Today, we will place the emphasis on the impact.
While impact alone is not everything, it will certainly help you decide whether a task should be automated or carried manually. Impact is one of the main drivers to take decisions.
What is impact?
Impact is defined as “a significant or strong influence; an effect”. When you start automating your day-to-day tasks, your actions and work will be significantly affected by the process.
Understanding the influence that Automation will have in your work is of paramount importance to decide whether to invest on it or not. Note that the impact is not necessarily always positive. You could be spending more time automating the process than if you were to do it manually, or producing something which is of a worse quality than the original process.
Hence, you should always pay attention to the results of automation.
Economic impact
Time savings
If you are considering automating a certain activity, you should start thinking: how much does this activity cost me? There are many factors involved; like human cost (hours paid to the employee), infrastructure costs (computers, electricity or office space) or material costs (resources required).
Ideally, when analysing the next task to automate, you would love to include all potential costs and savings into the model. However, this is sometimes not a straightforward calculation. In order to avoid complicating the model, a good solution is to start thinking in time savings.
In other words, a good proxy is to compare how much time the process was taking manually before and compare it to how much time they would take once automated.
Calculating time savings is as simple as calculating the times a task is performed in total (per time period) and multiplying it by the time it takes when it is performed:
If a workflow or task takes 30 minutes and it is carried 3 times a day by each of the 10 employees on the team, by the end of the day this will have costed you 900 minutes (30min x 3 times x 10 employees). This is the equivalent of 15 hours of work, or almost the full time of two of them (8h per day x 2 employees ≃ 15 hours). This might be a significant cost given the size of the team and might be something worth considering automation.
Once the impact is expressed in hours or full time employees, it can easily be translated to economic impact:
If the total yearly cost of an employee is $100,000 per year, and the process is saving 2 employees; the potential economic savings of the solution is $200,000 (2 employees x $100,000 per employee).
Note that the true economic impact of having employees running the task manually is not just their salary. It also includes taxes, benefits, building space, hiring, training, etc… However, you can start with an average salary cost to get an approximate translation to a monetary value.
Cost of opportunity
The cost of opportunity is an economic concept which describes the “the loss of potential gain from other alternatives when one alternative is chosen”. In other words, every time a decision is taken, there is an implicit cost derived from the benefits that could have been obtained from the alternatives.
When you allocate employee’s time to perform a task, the cost of carrying out the process is not simply the actual time of the employee (and all the other activity related costs); it includes the benefit you could be obtaining if their time was invested in a different fashion.
As a result, Automation does not impact only in savings, but it creates opportunities for tapping into benefits that were locked before due to capacity constrains.
In the case study of IEBSchool (IEBS), the newly created capacity allowed us to produce more materials and increase the portfolio of programs. This way the business was able to obtain new sources of income which were higher than the simple savings obtained from automating the workflow.
Using the example from the previous section, IEBS could reinvest the time savings into more profitable avenues:
The described process was consuming 2 full time employees. You could simply get rid of those roles and save $200,000. However, you could also re-invest these resources into spending more time with our customers and bring an additional $1M from sales. This would be the true value of automating the low-value tasks.
Non-economic impact
While economic impact is usually the main driver when deciding what processes should be automated, getting rid of manual and repetitive tasks has qualitative impact which is worth considering and expressing.
Quality and customer satisfaction
The first one to consider is quality. Humans are error-prone and may commit a significant number of mistakes when performing boring, repetitive and low-value added tasks. Automation can potentially increase the quality of the process by removing human errors derived from lack of attention or fatigue.
While it is hard to measure the long term net effect of improving the quality, it is definitely a desirable impact. Quality is also a factor which will impact the customer satisfaction on your product or services and may lead to more business in the long run.
In the opposite sense, the automation method does matter. Not all automations might be perfect and machines also can make mistakes. The process can be error prone and contain issues derived from the method, the code or simply not run reliably.
For example, if you automate a classification process using machine learning, the predictions will be statistically correct; which means that the results may have mistakes.
In this case, the quality output of humans vs machine should be compared and a decision should be taken on whether the change in quality is desirable. This is almost always true when it increases, but it might also be true even when it goes down if the savings are significant, or if a combined method (automation + manual) can out-weight the loss of quality at a lower cost than the original solution.
Employee satisfaction
Another key factor to consider is employee satisfaction. Performing manual and repetitive tasks is highly discouraging for everyone. It prevents you from using our full capacity to deliver on the highest value tasks that cannot be automated.
Getting rid of these tedious processes will have not only economic impact, but also boost your employees motivation. As explained on the “cost of opportunity” section, these employees will be able to focus on value-added tasks which will not only be positive for the business, but also for their motivation and retention.
The cost of automation
Until now we have been focusing on the “positive impact” of Automation and expressed it as both economic and non-economic factors.
However, automating a task also has costs which should be considered before taking a decision.
Time investment
Creating an automation solution requires time. Even for simple Automations which you can do yourself, you need to spend time creating or configuring the solution.
Not only this, but the solution may require maintenance along the months or years of its duration. APIs change frequently and the business needs do to. Hence, when calculating the costs, you should try to estimate also the time that it will require to maintain the solution throughout the year.
Similarly to the positive impact, hours invested can be translated into an economic cost by multiplying for the cost per hour. What is most relevant here is that maybe the resources invested in creating the solution (e.g. engineering time) might be more costly or more limited that the hours saved in automating.
Many companies may choose to externalise this cost and hire a vendor to create the Automation. However, the cost and logic behind its source does not change. This can be an effective solution when our own resources are constrained.
Resource cost
Beyond human or time investment, there are other resources which should be taking into consideration when calculating costs.
If you created a complex automation solution, you may need to pay for services to run the solution. This can go from as simple as paying a “premium” account in a service, to maintaining servers or paying cloud infrastructure. Regardless of your choice, you should include these costs on your calculations. The more advanced and robust your solution is, the more likely these costs will be significant (and probably also the larger impact of such automation).
Cost of opportunity
The cost of opportunity was explained when talking about the impact. However, it is also a factor to consider when talking about cost.
If your solution requires any kind of resources and the resources are limited (they usually always are), there is the possibility that using these resources for another purpose could yield higher results.
A common scenario of this happens when using Engineering resources. Creating an Automation solution may have positive and good return. However, these resources could have been used to create a different solution or a new product which could be bringing a lot more revenue or impact than what they are saving on the current solution. While this holds true for Engineering resources, it could also be the case for any other resources like investments (money), computer power, etc.
As a result, you should always take decisions having analysed and prioritised all the possible options (or as many as possible) in which you can leverage the resources. Analysing in isolation can help to understand the opportunity, but not to fully take the decision on where is the best place to invest resources.
Qualitative Costs
While more rare than economic costs, Automation could derive into qualitative costs (or, better said, have a negative impact).
Failures or inconsistencies on the automation process could result in a reduction of quality. For example, the process might be inconsistent and produce different levels of quality or with low reliability.
However, even when the actuality quality is good or superior, it may result in a perceived diminished value by your customers. For example, customers may perceive the new automated process as less human and, therefore, of lesser quality.
Conclusion
Automation is a highly valuable process for both businesses and professionals.
Removing manual and repetitive tasks will allow not only to save labor costs, but also to move the work up the value chain and produce higher benefits for the business. Additionally, automation can bring qualitative benefits such as increased employee satisfaction and quality.
However, automation also has associated creation and maintenance costs. As a result, when considering the automation of a process, one should not only consider the benefits, but also the cost and specially the return.
All in all, when contemplating the overall costs for creating and maintaining the solution you should ensure that the net impact is still significantly positive.